Safety in traffic control is paramount as it directly impacts the well-being of both the public and workers. Proper traffic control measures help to prevent accidents, manage traffic flow, and ensure the smooth operation of roadworks and construction sites. Inadequate traffic control can lead to severe consequences, including accidents, injuries, and fatalities.
Traffic control involves the strategic placement of signs, signals, barriers, and personnel to guide and manage vehicle and pedestrian movement safely. Ensuring safety in traffic control not only protects those directly involved in roadwork or construction but also ensures the safety of drivers, cyclists, and pedestrians who navigate through these areas daily.
Impact on Public and Worker Safety
Effective traffic control measures significantly reduce the risk of accidents and injuries. For the public, clear and visible traffic signs, signals, and barriers help in understanding and following temporary changes in road conditions, thus preventing confusion and accidents.
For workers, safety measures such as proper signage, barriers, and personal protective equipment (PPE) create a safer working environment. Workers are less likely to be injured when motorists are adequately informed and guided through the work zone. The implementation of comprehensive safety protocols also helps in minimizing the exposure of workers to hazardous conditions, ensuring that they can perform their duties safely.
Essential Safety Features of Traffic Control Equipment
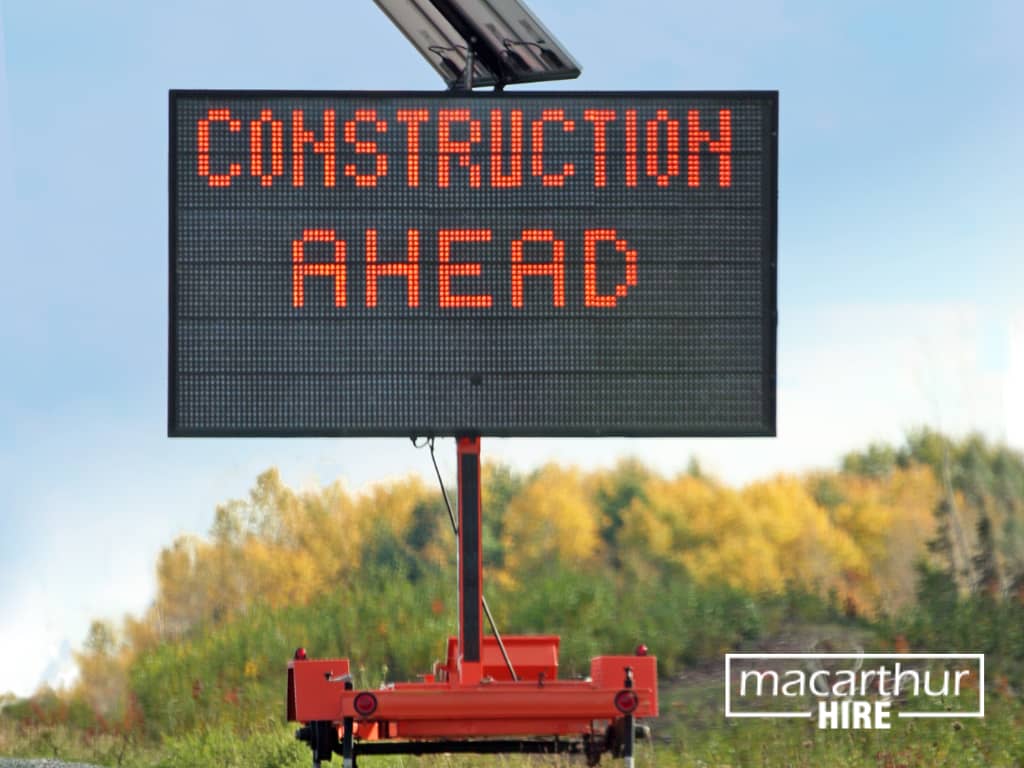
Standard Safety Features
Standards safety featuress in traffic control equipment are crucial in ensuring that the equipment performs its function effectively. Key safety features include:
- Reflective Materials: These are used extensively in traffic signs, barriers, and cones to ensure visibility, especially at night or in low-light conditions. Reflective materials help to catch the light from vehicle headlights, making the signs and barriers more noticeable to drivers.
- Stability Features: Traffic control equipment such as barriers and cones are designed to be stable and resistant to being easily knocked over. This includes weighted bases or interlocking systems that prevent equipment from being displaced by wind or minor impacts.
- Durability: Equipment must be made from durable materials that can withstand harsh weather conditions and constant exposure to traffic without deteriorating.
Innovative Safety Technologies
Advancements in technology have led to the development of innovative safety features that enhance traffic control:
- Smart Signs: These are electronic signs that can display variable messages to drivers, providing real-time updates about road conditions, traffic delays, and detours. Smart signs can be controlled remotely and updated as situations change, improving communication and safety.
- Automated Alert Systems: These systems can detect hazardous conditions, such as the presence of workers on the road or slow-moving traffic, and automatically alert drivers through flashing lights or audible alarms.
- Solar-Powered Equipment: Many modern traffic control devices are equipped with solar panels to ensure continuous operation without the need for a constant power supply, enhancing reliability and reducing maintenance costs.
Selecting Safe Traffic Control Equipment
Choosing Reliable Equipment Rentals
When selecting traffic control equipment from rental companies, it is essential to ensure that the equipment meets safety standards and is reliable. Here are some tips for selecting safe equipment rental:
- Research Rental Companies: Choose companies with a good reputation for providing high-quality, well-maintained equipment. Look for reviews and testimonials from previous clients.
- Verify Compliance: Ensure that the rental equipment complies with local and national safety regulations. The equipment should have the necessary certifications and meet the required safety standards.
- Ask About Maintenance: Inquire about the maintenance schedule of the equipment. Regular maintenance is crucial for ensuring that the equipment is in good working condition.
Evaluating Equipment Condition
Before using rented traffic control equipment, it is essential to inspect it thoroughly to ensure it is in safe working condition:
- Check for Damage: Inspect the equipment for any signs of wear and tear, damage, or defects. Ensure that all parts are intact and functioning correctly.
- Test Functionality: If possible, test the equipment to ensure it operates as expected. This includes checking the stability of barriers, the visibility of reflective materials, and the functionality of electronic components in smart signs.
- Confirm Specifications: Ensure that the equipment specifications match the requirements of your project. This includes the size, weight, and design of the equipment.
Maintenance and Inspection Protocols
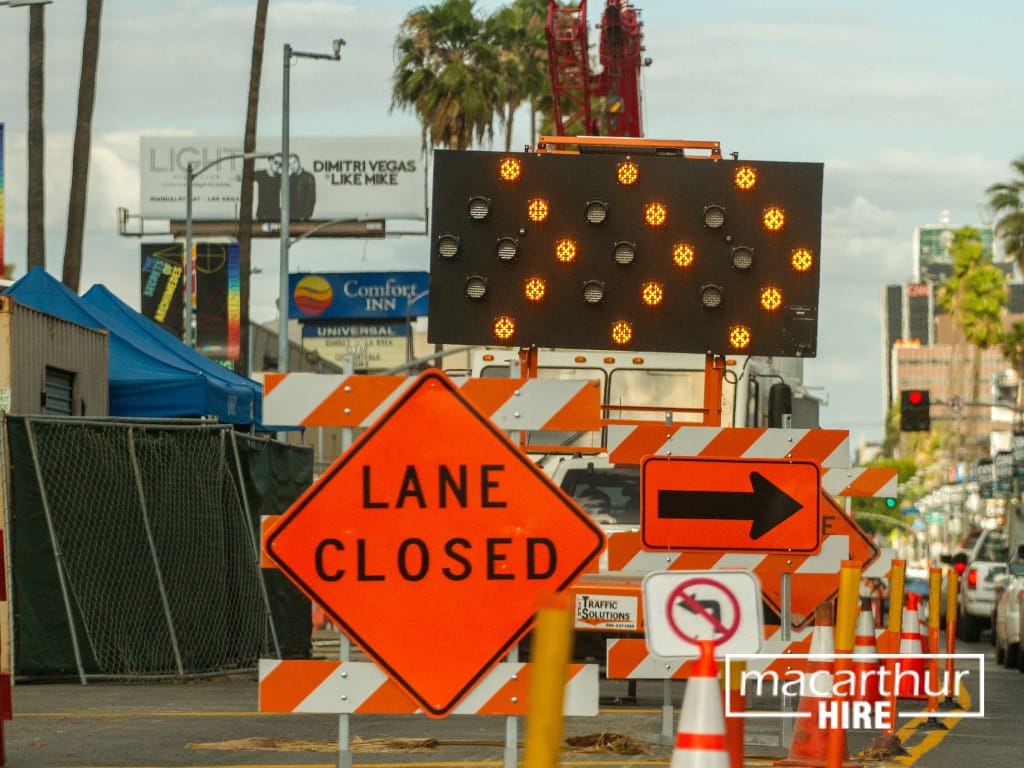
Regular Maintenance Checks
Conducting regular maintenance checks on rented traffic control equipment is essential for ensuring safety and operational efficiency. Regular maintenance helps to identify and rectify any potential issues before they lead to equipment failure or safety hazards. These checks should be scheduled routinely and include thorough inspections of all equipment components.
Key Points:
- Preventative Maintenance: Regularly scheduled maintenance can prevent unexpected equipment failures.
- Safety Assurance: Ensures that all equipment remains compliant with safety standards.
- Longevity: Regular maintenance extends the life of the equipment, making it more cost-effective over time.
Inspection Procedures
Detailed inspection procedures are necessary to ensure that all traffic control equipment is in safe working condition before use. These procedures should be comprehensive and follow a standardized checklist to cover all critical aspects of the equipment.
Inspection Checklist:
- Visual Inspection: Check for visible damage, wear, or defects in the equipment.
- Functionality Tests: Ensure all moving parts and electronic components are functioning correctly.
- Stability Check: Verify that barriers, signs, and other equipment are stable and secure.
- Reflectivity: For signs and barriers, check the reflectivity to ensure they are visible at night.
Training and Certification for Equipment Operators
Operator Training Requirements
Proper training for operators handling traffic control equipment is crucial for maintaining safety on site. Operators should be well-versed in the operation, maintenance, and emergency procedures related to the equipment they use.
Key Areas of Training:
- Equipment Operation: Detailed instructions on how to safely operate each piece of equipment.
- Safety Protocols: Training on safety measures and protocols to prevent accidents.
- Emergency Procedures: How to respond to equipment malfunctions or other emergencies.
Certification Programs
Certification programs provide formal recognition of an operator’s proficiency and understanding of traffic control equipment. These programs enhance safety and operational efficiency by ensuring that all operators meet a standardized level of competency.
Benefits of Certification:
- Professional Standards: Certification ensures that operators meet industry standards.
- Increased Safety: Certified operators are more likely to adhere to safety protocols.
- Regulatory Compliance: Certification helps in complying with local and national safety regulations.
Implementing Safety Protocols on Site
Site Safety Assessments
Conducting safety assessments on-site is essential for identifying potential hazards and ensuring that safety measures are in place. These assessments should be performed regularly and whenever there are significant changes to the site layout or conditions.
Assessment Steps:
- Hazard Identification: Identify potential safety hazards, such as blind spots or high traffic areas.
- Risk Evaluation: Evaluate the risks associated with each identified hazard.
- Mitigation Measures: Implement measures to mitigate identified risks, such as additional signage or barriers.
Emergency Response Plans
Developing and implementing emergency response plans is critical for handling accidents or equipment failures effectively. These plans should be comprehensive and well-communicated to all site personnel.
Components of an Emergency Response Plan:
- Emergency Contacts: List of contacts for emergency services and key personnel.
- Evacuation Procedures: Clear instructions on evacuation routes and procedures.
- First Aid Protocols: Procedures for providing immediate first aid to injured personnel.
- Equipment Shutdown: Steps for safely shutting down equipment in an emergency.
Compliance with Safety Regulations
Understanding Regulatory Standards
Ensuring the safety of traffic control operations requires a thorough understanding of the regulatory standards governing the use and maintenance of traffic control equipment. These regulations are designed to protect workers, drivers, and pedestrians by setting clear guidelines for the safe use of traffic control devices and equipment.
Key Regulatory Standards:
- National Standards: In many countries, national safety bodies such as OSHA (Occupational Safety and Health Administration) in the United States, set forth regulations for traffic control equipment. These standards cover everything from the design and placement of traffic signs to the required training for personnel.
- Local and State Regulations: In addition to national standards, local and state governments may have additional requirements. For example, the Department of Transportation (DOT) often provides guidelines specific to the state or region.
- Industry-Specific Guidelines: Certain industries, such as construction or event management, may have specific safety guidelines. These can include best practices for setting up temporary traffic control zones and using specialized equipment.
Important Regulatory Considerations:
- Equipment Specifications: Ensure all traffic control equipment meets the prescribed standards for durability, visibility, and functionality.
- Personnel Training: Operators and workers must be trained according to the regulatory standards to handle the equipment safely and effectively.
- Regular Audits: Conducting regular safety audits to ensure ongoing compliance with all regulatory standards.
Ensuring Compliance
Compliance with safety regulations is not just about adhering to laws but also about fostering a culture of safety within the organization. Here are strategies to ensure compliance:
Strategies for Ensuring Compliance:
- Documentation: Maintain detailed records of all safety training, equipment inspections, and maintenance activities. This documentation is crucial for demonstrating compliance during audits.
- Regular Training Updates: Ensure that all personnel receive regular training updates to stay informed about the latest safety standards and best practices.
- Safety Officer: Appoint a dedicated safety officer responsible for overseeing compliance with safety regulations and conducting regular inspections.
- Safety Protocols: Develop and enforce strict safety protocols for all traffic control operations. This includes emergency procedures, daily safety checklists, and routine maintenance schedules.
- Third-Party Audits: Periodically engage third-party auditors to conduct unbiased safety assessments and identify areas for improvement.
Conclusion
Maintaining safety in traffic control operations involves a multifaceted approach that includes understanding and complying with regulatory standards, regular maintenance and inspections, and ensuring that all personnel are properly trained and certified. By implementing these safety measures, organizations can significantly reduce the risk of accidents and enhance the overall efficiency and reliability of their traffic control systems.